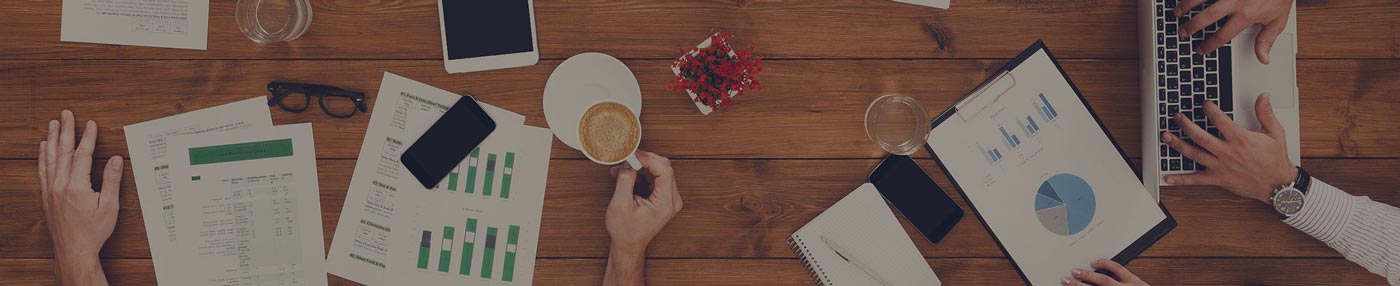
Close Calls
A “close call”, near miss or accident without injury is easy to shrug off and forget. But, there is a danger in brushing off accidents that don’t hurt, harm or damage. When a “close call” happens, it should immediately send a red warning flag that something was wrong, unplanned, unexpected, and could happen again. The next time it happens, it could result in serious damage, injury or death.
For every accident there are usually several contributing factors, most of which can be controlled. The best way to prevent the reoccurrence of an accident is by looking at those “close calls.” By investigating the root causes of an accident, steps can be taken to eliminate the hazard and improve the work system.
Sometimes there are multiple causes for an accident involving: equipment (unguarded machinery), environment (poor lighting or noise level), people (procedures not understood or not followed) or management (allowed shortcuts). Don’t rush to judge. Examine the facts and find what’s missing. Look for immediate and underlying causes. An immediate cause may be an unsafe condition like a mechanical failure or it could be an unsafe action by an employee. The underlying cause could be poor machine maintenance, a missing guard, a crowded work area or a lack of training.
All incidents must be reported to your employer Diversified Staffing and the site supervisor so that accident/injury report forms can be completed. Solutions should be sought to prevent the accident from occurring again and may involve engineering controls, administrative controls, additional training, or increased communication between management and workers.
Workers should inspect the work area daily for unsafe conditions or unsafe actions and, if found, report them to the supervisor. Hazard awareness is key to preventing accidents before they happen. Take steps to eliminate hazards as soon as they are discovered. The first step is to complete the Worksite Hazard Assessment Card. Learn the real lesson from close calls/near misses. They can happen again and again until they cause injury, so tell your employer and supervisor about every accident, no matter how minor it may seem at the time. You never know when an incident may be repeated and result in an injury or even death.
Attached to the back of your Diversified timecard you will find a Worksite Hazard Assessment Card. Please review and complete before you begin work. Completed hazard assessment cards are to be handed in with your timecard.
The purpose of the hazard assessment card is to identify hazards and eliminate/control which will help keep YOU the worker safe and prevent injuries.
As a Diversified worker you MUST assess the worksite and identify existing or potential hazards before work begins.
The hazard identification process is to be used for all job activities.
Thank you for supporting WORKPLACE SAFETY!